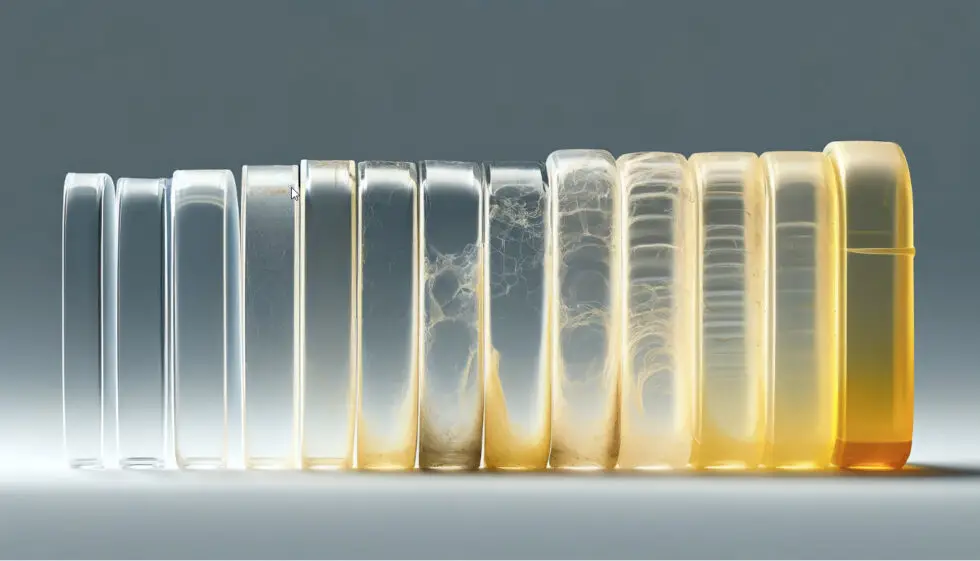
کاهش شفافیت و براقیت در PVC شفاف: ۵ علت رایج و راهحلهای صنعتی
شفافیت و براقیت در محصولات PVC نرم (مانند فیلمهای بستهبندی، شلنگهای پزشکی، و پوششهای تزئینی) نهتنها بر جذابیت بصری، بلکه بر ادراک کیفیت محصول تأثیر مستقیم دارد. مطالعات بازار نشان میدهد محصولات با شفافیت بالا می توانند تا ۳۰٪ گرانتر فروخته شوند. با این وجود، بسیاری از تولیدکنندگان حتی با فرمولاسیونهای ظاهراً استاندارد، با مشکلاتی مانند کدری (Haze)، کاهش براقیت (Gloss Loss) یا لکههای سفید مواجه میشوند. این مقاله به بررسی ۵ علت اصلی و ارائه راهکارهای عملیاتی میپردازد.
علت اول: استفاده از رزین PVC با K-value نامناسب شفافیت PVC را کاهش میدهد
عدد K-value (شاخص ویسکوزیته) نشاندهنده میانگین وزن مولکولی رزین PVC است. رزینهای با K-value پایین (مثل S60: K=60) زنجیرههای کوتاهتری دارند که باعث کاهش انعکاس نور و ایجاد کدری کلی میشود. رزینهای با K-value بالا (مثل S70: K=70) ساختار بلوری منظمتری ایجاد میکنند و شفافیت را افزایش میدهند.
راهکار صنعتی
- برای محصولات شفاف: PVC S65/67 (K=65-67) تعادلی بهینه بین شفافیت و فرآیندپذیری ایجاد میکند.
- از رزینهای Suspension Grade با توزیع ذرات باریک (مثل ۹۰-۱۱۰ میکرون) استفاده کنید تا نور کمتری پراکنده شود.
علت دوم: استفاده از نرمکننده (Plasticizer) نامناسب یا ناخالص
نرمکنندههای فتالاتی (مثل DOP) با خلوص پایین حاوی مونومرهای واکنشناپذیر هستند که پس از اختلاط، لکههای کدر ایجاد میکنند. نرمکنندههای خطی (مثل DINP/DINCH) نسبت به DOP شفافیت بالاتری دارند اما ممکن است با PVC نا سازگاری شیمیایی نشان دهند. وجود رطوبت یا اسیدهای آلی در نرمکنندههای بازیافتی موجب هیدرولیز PVC و کدری میشود.
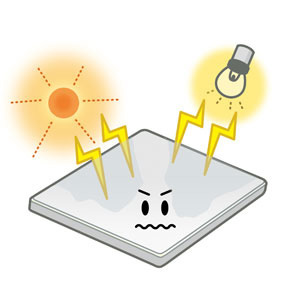
راهکار صنعتی
- استفاده از DOTP گرید خلوص بالا (اسیدیته ≤ ۰.۰۱٪، رطوبت ≤ ۳۰۰ ppm).
- جایگزینی با پلیاستر پلاستیسایزرها (مثال: Hexamoll DINCH) برای کاربردهای پزشکی با شفافیت حداکثری.
- تست سازگاری نرمکننده با PVC: قرار دادن نمونه در دمای ۶۰°C به مدت ۷۲ ساعت و بررسی تغییر رنگ/شفافیت.
علت سوم: پخش نامناسب افزودنیها سبب کاهش براقیت PVC میشود
ذرات استابلایزرهای کلسیم-روی یا آنتیاکسیدانتها اگر کاملاً پخش نشوند، به عنوان مراکز پراکندگی نور عمل میکنند. پرکنندههای معدنی (مثل کربنات کلسیم) با توزیع اندازه ذرات گسترده (>۵ میکرون) نقاط مات ایجاد میکنند.
راهکار صنعتی
- استفاده از مستربچهای پلیمری حاوی افزودنیهای پخششده در پایه PVC (کاهش اندازه ذرات تا ۱-۲ میکرون).
- بهینهسازی فرآیند اختلاط:
- میکسرهای پرسرعت (High-Speed Mixer): دمای ۱۲۰°C به مدت ۸-۱۰ دقیقه.
- بانبوریهای دو محوره (Banbury Mixer): برش مکانیکی شدید برای شکستن کلوخهها.
علت چهارم: فرمولاسیون حاوی پرکننده یا افزودنی ناسازگار
پرکنندههای معدنی: حتی مقادیر >۲ phr کربنات کلسیم با اندازه ذرات >۳ میکرون، شفافیت را تا ۴۰٪ کاهش میدهد. مواد بازیافتی: PVC بازیافتی حاوی ناخالصیهای پلیمری (مانند PET یا PP) که Haze ایجاد میکنند. روغنهای فرآوری: باقیمانده روغنهای رهاساز (Release Agents) روی سطح مهاجرت میکنند.
راهکار صنعتی
- جایگزینی پرکنندهها با کربنات کلسیم پوششدار استئاریک اسید (اندازه ذرات ≤ ۱ میکرون).
- افزودن کوپلیمرهای اکریلیک (مثال: Paraloid K-120N یا KANE ACE P550) به میزان ۰.۵-۱ phr: بهبود شفافیت با کاهش ضریب شکست.
- محدود کردن مواد بازیافتی به ≤ ۱۵٪ و استفاده از جداسازندههای الکترواستاتیک برای حذف ناخالصیها.
علت پنجم: دما و زمان نامناسب در فرآیند
خطاهای رایج در فرآیند:
- اکستروژن: دمای بیش از ۱۹۰°C در ناحیه ذوب (Melt Zone) باعث تخریب حرارتی و زردی/کدری.
- کلندرینگ: سرعت غلطکهای نامناسب → کشش سطحی ناهمگن → کاهش براقیت (Gloss < ۸۰٪).
تنظیمات بهینه:
فرآیند | پارامتر | مقدار مطلوب |
---|---|---|
اکستروژن | دمای ناحیه ذوب | ۱۷۵-۱۸۵°C |
فشار دای (Die) | ۲۵۰-۳۵۰ بار | |
کلندرینگ | دمای غلطک میانی | ۱۶۵-۱۷۰°C |
اختلاف سرعت غلطکها | ≤ ۱۵٪ |
جدول خلاصه مشکلات و راهکارهای حل معضل کدر شدن PVC
در جدول زیر راهکارهای افزایش شفافیت و براقیت PVC های شفاف به صورت خلاصه آورده شده است:
علت | نشانه ظاهری | راهکار فنی |
---|---|---|
رزین نامناسب | کدری یکنواخت | PVC S67 با K-value=67 |
نرمکننده ناخالص | لکههای ابری | DOTP خلوص ۹۹.۸٪ + تست جذب آب (ASTM D1364) |
پخش ضعیف افزودنی | نقاط ریز مات | مستربچ حامل + اختلاط پرسرعت (۱۰۰۰ rpm) |
پرکننده زیاد | سطح شیری رنگ | کربنات کلسیم ۱ میکرون + کوپلیمر اکریلیک |
خطای فرآیندی | براقیت ناهمگن | کالیبراسیون اکسترودر + تنظیم اختلاف دمای زونها |
نتیجهگیری
کاهش شفافیت PVC شفاف، اغلب ناشی از تعامل پیچیده مواد اولیه و پارامترهای فرآیندی است. راهکارهای پیشنهادی این مقاله مبتنی بر تستهای صنعتی (مثل ASTM D1003 برای Haze و ASTM D2457 برای Gloss) و دادههای تولید انبوه طراحی شدهاند. برای دستیابی به محصولی با شفافیت >۹۰٪ و براقیت >۸۵٪:
۱. از مواد درجهیک با گواهی آنالیز (COA) استفاده کنید.
۲. فرمولاسیون خود را توسط متخصصان ما بهصورت رایگان بهینهسازی کنید.
۳. نمونه افزودنیهای شفافکننده (مانند ARKEMA P550) را برای تست دریافت نمایید.
📞 برای مشاوره تخصصی و دریافت راهنمای فرمولاسیون PVC شفاف، با شماره 09124042344 تماس بگیرید.
یک نظر
مفید بود ممنون